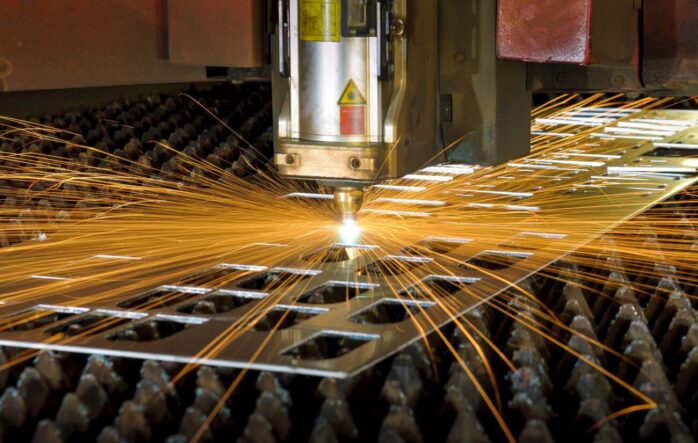
The world of manufacturing has been revolutionized by laser-cutting technology. This high-precision, efficient, and environmentally friendly process has transformed industries ranging from automotive to aerospace, medical to metalworking.
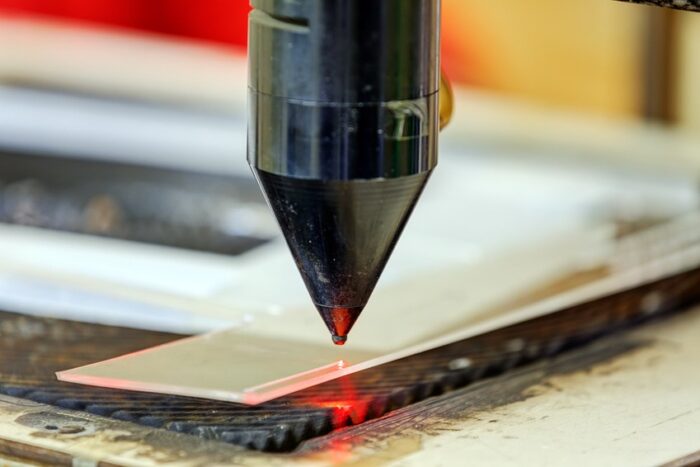
The Basics
Laser cutting is a non-contact manufacturing process that uses a focused, high-powered beam to cut or engrave materials with extreme precision. The beam is generated by a laser source, which can be either a gas-based (such as CO2) or a solid-state laser (such as fiber or crystal lasers). The beam is directed through a series of mirrors and lenses, finally being focused on the material to be cut. The heat generated by the beam causes the material to melt, burn, or vaporize, creating a smooth, clean-cut edge.
The key advantages of laser cutting technology include:
- High precision and accuracy: The beam can be focused down to a diameter as small as 0.001 inches, enabling intricate designs and tight tolerances.
- Versatility: Laser cutting is compatible with a wide range of materials, including metals, plastics, wood, textiles, and composites.
- Speed: The process is typically faster than traditional cutting methods, reducing production time and costs.
- Minimal material waste: The narrow kerf width and non-contact nature of the process result in minimal material waste, maximizing material usage and minimizing environmental impact.
Designing The Product
The first step in the process is creating a digital design. This design serves as a blueprint for the laser cutter, guiding the movement of the beam as it cuts the material. To create a design, follow these steps:
- Choose the right software: Popular software options for designing laser cutting projects include Adobe Illustrator, Inkscape, AutoCAD, and SolidWorks. These programs allow you to create vector-based designs, which are essential for controlling the laser cutter’s path.
- Convert your design into a vector file: Vector files (such as .SVG, .DXF, or .AI) contain geometric data that can be scaled without losing quality. This is important for achieving precise cuts and maintaining design integrity at various sizes.
- Optimize your design for laser cutting: Consider factors such as material thickness, kerf width, and minimum feature size when designing your project. This will ensure that your design is compatible with the process and that the final product meets your expectations.
Choosing the Right Cutter for Your Project
Selecting the appropriate laser cutter for your project is crucial to achieving the desired results. Factors to consider when choosing a laser cutter include:
- Power: Higher-power lasers can cut through thicker materials and at faster speeds, but they may also be more expensive to operate and maintain.
- Laser type: CO2 lasers are versatile and suitable for cutting a wide range of materials, while fiber lasers are ideal for cutting metals due to their higher energy density and lower operating costs.
- Bed size: The bed size determines the maximum dimensions of the material that can be cut. Choose a cutter with a bed size that accommodates your project requirements.
- Software compatibility: Ensure that the cutter you select is compatible with the design software you plan to use. This will streamline the process and minimize potential issues during production.
- Budget: Laser cutters can vary significantly in price, so consider your budget when making your decision. Also, factor in the cost of consumables, maintenance, and power consumption.
Material Selection and Preparation
When working on a project, the material you choose is crucial because it affects the quality, speed, and overall outcome of the cutting process. For laser cutting, you should consider the type of material you want to use. Laser cutting is compatible with various materials such as metals (e.g., stainless steel, aluminum, copper), plastics (e.g., acrylic, polycarbonate), wood (e.g., plywood, MDF), textiles (e.g., leather, felt), and composites (e.g., carbon fiber, fiberglass).
The thickness of the material also plays a significant role in determining the cutting speed and laser power requirements. Thicker materials generally require more powerful lasers and longer cutting times.
Additionally, it is essential to consider the material’s properties such as melting point, thermal conductivity, and reflectivity, as these factors affect the cutting quality and efficiency.
Before cutting, you need to prepare the material correctly by cleaning the surface to remove any dirt, grease, or debris that could prevent a clean cut and cause contamination. You also need to secure the material to the laser cutter’s bed to prevent movement during the cutting process. Finally, adjust the focal point of the cutter according to the material’s thickness and properties to optimize cutting performance.
The Cutting Process
Adjust the cutting parameters, including the cutting speed and laser power, according to the material and desired outcome. Conduct a test cut on a scrap piece of the same material to ensure that the settings are correct and the desired cut quality is achieved. Start the process and monitor its progress to ensure that the design is being cut accurately and without any issues. After the cutting process is complete, carefully remove the cut pieces from the cutter’s bed.
Following the process, you may need to perform some post-processing and finishing steps to achieve the desired final product. Clean the cut edges by removing any residue, such as smoke deposits or melted material, from the cut edges using a brush, cloth, or compressed air. Inspect the quality of the cut pieces for any defects or inconsistencies, and make any necessary adjustments to the cutting parameters before proceeding with the rest of the production. Depending on the material and desired appearance, apply finishing techniques such as sanding, polishing, painting, or varnishing to enhance the final product’s aesthetics and durability
Conclusion
Laser-cutting technology has transformed the manufacturing landscape by offering a precise, efficient, and environmentally friendly alternative to traditional cutting methods. By understanding the entire process, from design to finished product, you can harness the power of this technology to create intricate and high-quality products in a diverse range of materials. By staying informed about the latest advancements in laser technology and adhering to best practices, you can ensure a successful and safe laser-cutting experience.