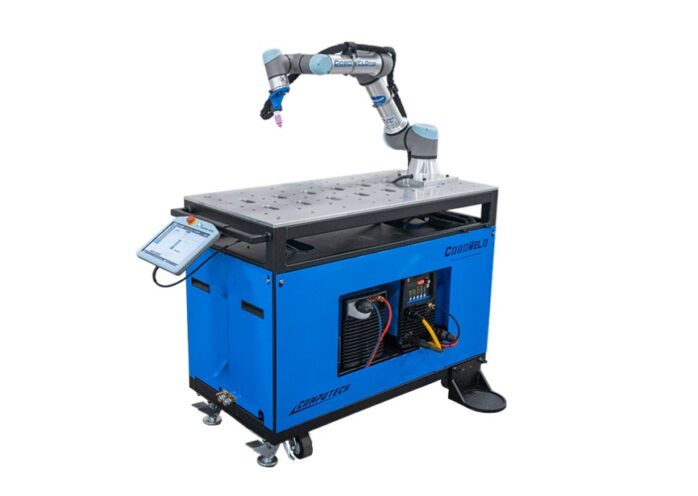
As industries evolve, the demand for precision and efficiency in manufacturing has never been greater. In sectors like automotive, aerospace, and construction, welding is a crucial process that requires accuracy and consistency to produce reliable, high-quality products.
Traditionally, welding has been a manual task, prone to inconsistencies and errors due to human limitations. However, recent advances in robotic technology, particularly in welding robots and other welding automation tools, are revolutionizing the field, enhancing precision, and transforming the manufacturing landscape.
The Importance of Precision in Welding
Welding plays a foundational role in assembling components for a variety of industries, from cars and airplanes to electronics and construction materials. In these sectors, precision in welding is not just a luxury; it’s a necessity. When welds are precise, the result is stronger, safer, and longer-lasting products, which is especially vital in high-stakes fields like aerospace and automotive.
Manual welding, however, has its limitations. Even experienced welders can be subject to fatigue, resulting in subtle inconsistencies that affect the final product’s integrity. Precision becomes critical when dealing with high-stress applications, as even the slightest deviation can weaken a weld, compromising the structural integrity of an entire assembly. Robotic arms offer a solution to these challenges, performing tasks with unmatched accuracy, consistency, and speed.
How Robot Arms Are Transforming the Welding Process
The rise of robotic arms in welding brings a new level of accuracy that’s difficult to achieve manually. Today’s advanced robotic arms are equipped with technologies like AI, machine learning, and adaptive sensors, enabling them to fine-tune their actions in real-time. These advancements are not limited to a single type of robot but extend to various categories, each suited to different applications:
- Articulated arms ─ With multiple joints, these arms can maneuver with a high degree of freedom, making them ideal for complex welding tasks.
- Cartesian robots ─ Known for their linear motion, these robots excel in precise, repetitive tasks that require high accuracy.
- Collaborative robots (cobots) ─ Designed to work alongside humans, cobots bring flexibility and can handle intricate, detailed welding in close cooperation with human workers.
Each of these robot types has its own benefits, and they’re all equipped with innovative tools like laser-guided systems and force-sensitive feedback, ensuring that welds are not only precise but adaptable to various materials and environmental conditions.
Features of Advanced Welding Robots
One of the most revolutionary features of advanced welding robots is the integration of high-resolution sensors that allow for real-time monitoring and adjustment. These sensors detect slight deviations, compensating for any movement or environmental changes that could impact weld quality. This instant feedback loop is critical in maintaining the accuracy required for high-stakes applications.
Adaptive Motion Control
Modern robotic arms are equipped with adaptive motion control, a technology that allows them to make micro-adjustments mid-process. Whether adjusting speed, pressure, or angle, these robotic arms can respond to real-time feedback, ensuring consistent weld quality. This capability is especially useful when welding complex geometries or performing tasks in confined spaces where precision is key.
Computer Vision and AI Integration
By integrating computer vision and AI, robotic arms can detect inconsistencies, defects, or other issues as they work. For instance, if the robot’s sensors detect a gap that’s wider than expected, the robot can adjust the weld parameters to fill the gap accurately. This technology is particularly useful in a TIG welding robot, where precision is paramount, and any flaw can compromise weld integrity.
Multi-Axis Capabilities
Many modern robotic arms come with multi-axis capabilities, allowing them to reach difficult or previously inaccessible areas with ease. This flexibility enhances their ability to weld complex components, making them ideal for applications in automotive, aerospace, and even electronics manufacturing.
Benefits of Using Robotic Arms for Precision Welding
When it comes to repetitive tasks like welding, robots outshine human workers in both accuracy and consistency. With every weld performed identically, robotic arms ensure high uniformity across production lines. This increased accuracy reduces defects and rework, saving time and materials.
Enhanced Safety for Human Workers
Welding can expose workers to various hazards, including extreme heat, toxic fumes, and physical strain from repetitive movements. By automating welding tasks with robotic arms, companies can reduce these risks, creating a safer working environment for employees. Human workers can then focus on overseeing the robots, further enhancing operational safety.
Reduced Material Waste
Precision welding leads to less material waste, as fewer errors mean fewer scrapped parts. By eliminating over-welding or under-welding, robotic arms optimize the amount of material used, reducing waste and lowering costs.
Cost Efficiency and Productivity Gains
While robotic arms require an initial investment, their ability to perform tasks quickly, accurately, and consistently leads to significant cost savings over time. They can work continuously without breaks, increasing productivity and ensuring that deadlines are met. Companies that implement robotic welding systems often see a high return on investment due to the cumulative cost savings from reduced labor costs, minimized errors, and increased throughput.
Conclusion
Advanced robotic arms are transforming the field of welding, offering unprecedented precision, safety, and efficiency. With features like high-resolution sensors, adaptive motion control, and AI integration, these robots ensure that welds are consistent and reliable, regardless of the complexity of the task. As industries continue to demand higher levels of precision, robotic welding arms will remain at the forefront, redefining what’s possible in manufacturing and engineering.