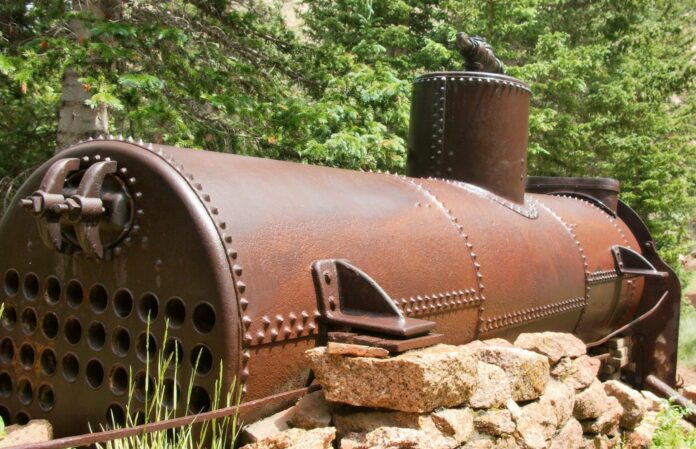
When it comes to any equipment, we always take into account its efficiency and overall performance. It matters most, primarily when we highly use it for mass production and assign it to perform loaded and heavy workloads. That very same philosophy is applied to boilers as industrial equipment.
But how can it be maximized to its optimum? Here, we will discuss the significant factors that affect a boiler’s performance and some few tips on how to increase its efficiency on the side.
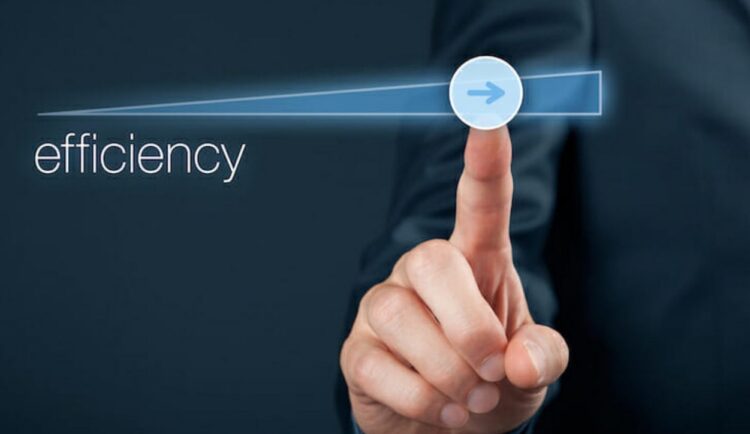
What is boiler efficiency?
In simple words, boiler efficiency is a measurement of the amount of combustion energy that is converted into steam energy. According to the ASME Energy Balance Method, some factors affect the calculation of boiler efficiencies such as stack, radiation, and convection losses.
Even though boiler design is still a major factor, there are other principal factors that affect boiler efficiency calculation. The main focus is to create a condition where there will be an increase in boiler efficiency by understanding the factors that mainly affect it.
5 Factors That Affects A Boiler Efficiency
Despite boilers having different designs, they have a common denominator when it comes to their efficiency. And determining and understanding what these factors are can help you recognize and resolve boiler issues that you will encounter in the future. Even more so, it allows you to make a solution to have your system reach optimization.
1. Flue gas temperature
A flue gas or exhaust gas is a gas that has been expelled during boiler operation. If the flue gas temperature is high, that means that the heat produced during the boiler operation is not used to create steam, hence it is lost. The resolution for this situation is to create a condition that will keep the flue gas temperature at its possible lowest temperature.
If your boiler keeps on releasing a high-temperature flue gas, then you are on the losing side. According to Wirral Plumbers, you should have a professional install combustion air heaters or economizers. Economizers for one can help to save fuel and the possible damage that cold water can do to your boiler.
When you are renting a boiler, make sure to ask questions if they have an economizer. You can contact ctcair.com when you need to rent one. They can further assist you with these kinds of measures to increase boiler efficiency.
2. Fuel Specification
If you were thinking of less about fuel specification, then think again. Determining the right fuel specification should be given the utmost priority. Addressing this issue is simple as you only need to establish the right fuel specification and make sure that the actual fuel meets the criteria. The most common fuel types used in boilers are natural gas, fuel oil, coal, and wood (biomass).
It is worth noting that fuel specification plays a vital role in increasing boiler efficiency. Remember that the higher the hydrogen content, the more water vapor is formed during the combustion process. Therefore, high water vapor losses and lower efficiency. To solve this, have a natural gas combined with higher methane concentrations and lower content of other gases. This equation will burn much more efficiently and can operate at a higher efficiency.
3. Excess Air
If there’s an increase of excess air in the combustion chamber, this will all absorb all the energy from the fuel, which can still be used to raise steam. Therefore, it will result in lower boiler efficiency. An increase in excess air is present when there is a rise of flue gas temperature, which indicates a heat loss during the boiler operation.
However, some cases require excess air during the combustion process. One example is an ultra-low-emission burner, the excess air is utilized to reduce the production of carbon monoxide and NOx. This process is mainly to control the temperature of the flame.
4. Steam Losses
A well-maintained and regularly checked boiler produces high steam energy, but when the production is failing or losing, there is something wrong in the system. When there is less steam energy created, there is a steam loss. This happens when steam or hot water is allowed to escape due to leak in piping. Steam traps are commonly the reason why there is a steam loss. Frequent equipment checkup and maintenance can help avoid this situation from happening.
5. Radiation and Convection Losses
These losses are the only two factors that affect boiler efficiency that no one can prevent. They are inevitable factors when you use an industrial boiler. However, there are ways to minimize the losses.
The radiation and convection losses are the heat being released from the boiler during the operation. By properly insulating an industrial boiler, you can minimize its surface temperature and lower heat losses. You can do two effective strategies to reduce these losses, such as:
- Install a superior insulation method and make sure to utilize quality insulating materials as bad conductors help reduce heat loss by conduction.
- Control the airflow over the boiler surface. Shield your boiler from outdoor winds and indoor drafts are helpful.
Takeaway
There’s a lot of advantages when you start utilizing boilers for your business. However, just like other machines and equipment, they also have disadvantages as they are bound to factors that can cause their inefficiency. Yet, these inefficiencies have their contingencies as well. When you have the knowledge and the understanding of what causes the inefficiencies, you will know how to resolve them.