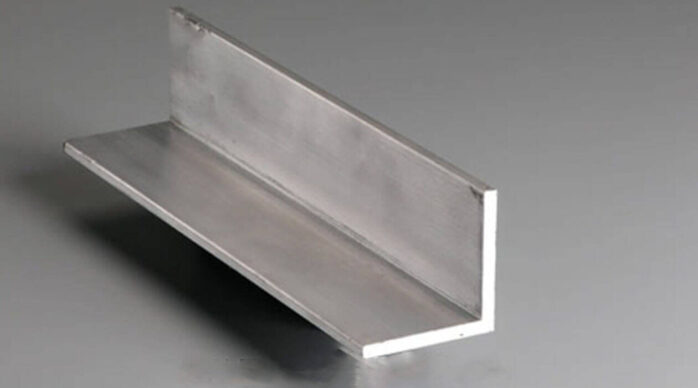
If you are glimpsing for a quality metal extrusion that can withstand the test of time, then 7075 aluminum extrusion is the best option available. This material is made up of 98% aluminum and 2% zinc, making it strong yet lightweight.
It has a variety of applications in both the commercial and residential sectors. In this guide, we will discuss the many benefits of using 7075 aluminum extrusion and provide tips on how to select the proper supplier.
What Is 7075 Aluminum Extrusion and What Are Its Uses
7075 aluminum extrusion is a process by which bars or rods of aluminum are forced through a die of the desired cross-sectional shape. The aluminum is warmed to make it more pliable and then passed through the die.
The resulting product has a uniform cross-section and can be used in a variety of applications. One common use for 7075 aluminum extrusion is in the construction of aircraft and spacecraft components.
The material is also frequently used in the manufacture of sporting goods, such as baseball bats and golf clubs. In addition, aluminum extrusion is often used in the production of high-strength parts for automobiles and machinery. Thanks to its unique combination of strength and durability, aluminum extrusion is one of the most versatile materials available.
Some Common Uses of 7075 Aluminum Extrusions Include:
- Construction: aluminum is often used in the construction of aircraft and other high-performance vehicles. Its strength and durability make it a perfect choice for these applications.
- Automotive Parts: aluminum is also commonly used in the manufacturing of automotive parts. Its strength and corrosion resistance make it a good choice for components that are exposed to the elements.
- Marine Applications: aluminum is also popular for use in marine applications, where its corrosion resistance makes it ideal for use in wet environments.
- Sports Equipment: aluminum is strong and durable, making it a good choice for sports equipment such as bicycles, skateboards, and snowboards.
The Benefits of Using 7075 Aluminum Extrusions in Your Projects
7075 aluminum is a popular choice for both home and commercial projects due to its many benefits. 7075 aluminum is significantly stronger than other types of aluminum, making it ideal for applications where strength is critical. In addition, 7075 aluminum is resistant to corrosion, making it a good choice for outdoor projects.
The high strength-to-weight ratio of 7075 aluminum also makes it ideal for applications where weight is a concern, such as in aircraft construction. Overall, 7075 aluminum offers an excellent balance of properties that make it a versatile material for a wide range of applications.
Standard benefits:
- Stronger than other types of aluminum
- Resistant to corrosion
- High strength-to-weight ratio
Emotional benefits:
- Ideal for applications where strength is critical
- Perfect for outdoor projects
- Ideal for projects where weight is a concern
The Manufacturing Process of 7075 Aluminum Extrusion
7075 aluminum is a high-strength alloy that is frequently used in the aerospace industry. In order to create extruded parts from this material, manufacturers must first heat the aluminum to its melting point. Once it is in a liquid state, it can be passed through a die, which gives it the desired shape.
After the aluminum has cooled and hardened, it can be cut to the desired length and then machined or otherwise finished as needed. The entire process of aluminum extrusion is typically completed within a matter of hours, making it an efficient way to produce parts for a wide range of applications.
FONNOV ALUMINIUM is your reliable supplier on manufacturing 7075 aluminum extrusions.
The Different Alloys That Can Be Formed Using the Extrusion Process
Extrusion is a procedure used to create objects of a fixed cross-sectional profile by forcing material through a die. One of the benefits of extrusion is that it can be used to create a wide variety of alloys. By varying the composition of the starting material, it is possible to produce alloys with a range of different properties.
For example, aluminum alloys extruded at high temperatures are typically stronger and more ductile than those extruded at lower temperatures. By adding other metals such as magnesium, silicon, or copper, it is also possible to create alloys with improved corrosion resistance or electrical conductivity. As a result, the extrusion process provides a versatile way to create materials with a wide range of desired properties.
Various Finishes That Can Be Applied to 7075 Aluminum Extrusions
When it comes to aluminum extrusions, there are a variety of finishes that can be applied in order to achieve the desired look and level of protection. 7075 aluminum is particularly popular for its strength and durability, making it a good choice for a variety of applications.
Common finishes for 7075 aluminum include anodizing, powder coating, and wet painting. each of these finishes provides different benefits in terms of appearance, durability, and cost.
Anodizing is a popular finish for aluminum extrusions because it creates a durable, protective layer on the surface of the metal. This layer helps to resist corrosion and scratching, making it ideal for high-use applications.
Anodized aluminum extrusions also have an appealing shiny finish that can be tinted in a variety of colors. While anodizing is more expensive than some other finishes, it is still relatively affordable and provides excellent protection for the metal.
Powder coating is another popular finish for aluminum extrusions. Powder coating provides a thick, durable finish that is resistant to scratches, fading, and corrosion. Powder coating is available in a wide range of colors, making it easy to find the perfect match for your project. While powder coating can be more expensive than anodizing, it does provide superior protection against the elements.
Wet painting is the most inexpensive option for finishing aluminum extrusions. Wet painting provides a basic level of protection against corrosion and scratching, but does not offer the same level of durability as anodizing or powder coating.
Wet painting is available in a wide range of colors, making it easy to find the perfect match for your project. However, wet-painted aluminum extrusions are more susceptible to damage from the elements and may require more frequent maintenance or replacement than extrusions with other finishes.
How To Select the Right 7075 Aluminum Extrusion for Your Needs
7075 aluminum extrusion is a popular choice for a wide range of applications, from aircraft construction to automotive parts. But with so many options on the market, how do you know which one is right for your needs? Here are a few factors to keep in mind when selecting an aluminum extrusion:
- The first step is to consider the dimensions of the extrusion. You’ll need to know the width, height, and thickness of the piece you need.
- Next, take a look at the tolerances. What level of precision do you need?
- Third, consider the surface finish. Anodized or powder-coated finishes can provide better wear resistance.
- Finally, think about what type of end treatment you need. Would threaded holes or cutouts be helpful?
By considering these factors, you can narrow down your options and choose the right aluminum extrusion for your needs.